О нас пишет пресса: Южноуральские машиностроители превращают металлолом в станки
Завод, где проводят полную модернизацию изношенного оборудования, расположен практически в чистом поле. И к нему ведет единственная асфальтовая дорога — не заблудиться.
Сначала продавали
Предприятие «Техинвест» значилось в программе рабочей поездки главы региона Бориса Дубровского в Красноармейский район. И это было не просто знакомством с машиностроителями. Этот проект можно назвать удачным примером внутренних инвестиций, рассчитанных на долгую перспективу. Именно такие бизнес-проекты отвечают Стратегии развития Челябинской области, которые сам Дубровский назвал «инвестиционным патриотизмом».
На следующий день мы вновь оказались на заводе, чтобы своими глазами увидеть, как из, по сути, списанных агрегатов рождаются современные станки. По заверениям руководителей предприятия, они могут вдохнуть вторую жизнь практически в груду металлолома. А сам бизнес начинался с продажи оборудования. Позже пришло понимание, что более перспективным для себя определили рынок ремонта и модернизации. Массивные основы станков сделаны практически на века, замены требуют лишь электронная начинка да эксплуатационные компоненты, как того требует технология.
— По сути, сегодня не осталось заводов, которые могли бы изготавливать громоздкие литейные конструкции, — объясняет заместитель директора Александр Яшкин.— Для потребителя однозначно дешевле приобретать восстановленные станки, которые полностью бы соответствовали современным нормам точности, расширенным возможностям обработки, даже таким параметрам, как потребление электроэнергии.
В ожидании своей очереди на реанимацию в цехе стояли десятки станков с числовым программным управлением, токарно-карусельные, фрезерные отечественного и импортного производства. Еще десятки механизмов, укрытые полиэтиленовой пленкой, стояли на площадке рядом с цехом. Большинство станков произведено в середине прошлого века, но после капремонта и переоснащения они готовы дать фору многим нынешним аналогам. Опережая их по ценовой категории и не отставая по техническим характеристикам.
Четыре знака после точки
Такова
точность обработки на станках, реанимируемых на предприятии. В качестве
примера нам показали по-своему уникальный токарно-карусельный
двухстоечный станок, который может обрабатывать сферические поверхности
диаметром свыше трех метров. После модернизации он несколько расширил
свои функциональные возможности.
— Такие станки востребованы на многих крупных машиностроительных предприятиях, — объясняет Александр Викторович. — Они используются для съемки кромок, обработки любых цилиндрических поверхностей, сварных конструкций.
— Сам станок произведен более 30 лет назад на заводе имени Седина в Краснодаре, — говорит инженер-электронщик Леонид Рябов. — Мы отшлифовали направляющие, восстановили геометрическую точность, поставили сервопривода, бесступенчатую регулировку. Чтобы не было головных болей у механиков, модернизировали коробку скоростей, убрав электромагнитные муфты. Встроили систему числового программного управления и теперь станком управляет на рабочий, а оператор.
Тут нужно добавить, что от рабочего теперь потребуется и инженерное образование, чтобы справиться с этим механизмом. О высокоточности станка можно судить по тем данным, что выводятся на дисплей: на табло он выдает еще четыре знака после миллиметровой точки, показывая десятитысячные доли миллиметра. Восьмидесятитонная махина обрабатывает трехметровые заготовки с точностью до десятой доли микрона.
Определяя свой спектр деятельности, на предприятии имеют четкое понимание, — кто является их конечным потребителем. От Дальнего Востока и до Центральной части России, где сейчас трудятся наладчики. Как образно выразился замдиректора, станки они сдают «под ключ». Выкупая на реконструкцию ржавый остов, они отправляют машиностроителям современный станок, монтаж и наладку проводя собственными силами. Приходилось ездить бригадам наладчиков и в Белоруссию, и в Корею.
На грани износа
Главе
региона Борису Дубровскому продемонстрировали один из станков, который
был выкуплен за 400 тысяч рублей, а сейчас его цена составляет 2,5
миллиона рублей. Это стоимость труда специалистов и самых современных
возможностей оборудования. Токарно-карусельный стоил 600 тысяч рублей,
а финальной цены пока нет — все зависит от тех заявленных возможностей,
которые затребует покупатель.
Но у покупателя есть выбор. Поддерживать ли отечественного производителя и экономить свой бюджет, либо отдать предоставленную государством субсидию на заграничный станок.
— Японская станкостроительная компания «Фанук» освобождена от налога на основные средства, не платят они и налог на землю, — перечисляет возможные государственные «поблажки» Леонид Рябов. — А кредит на развитие им выдают под 0,3 процента годовых! На неограниченный срок! И еще, насколько я знаю, на период разработки они не платят по кредиту.
Владимир Гутенев, первый вице-президент и первый заместитель председателя «СоюзМаш России» в одном из интервью подчеркнул, что уровень развития станкостроения — это ключевой фактор обеспечения промышленной конкурентоспособности.
— Станкостроение, в полном смысле, — синоним создания новых технологий. Оно определяет энергоэффективность и материалоэффективность промышленного производства, а значит, и его себестоимость, — заявил Гутенев. — Продукция станкостроения обладает свойством мультипликации: 1 рубль продукции станкостроительного завода создает потом 50–100 рублей промышленной продукции. В целом же государство, вкладывая инвестиции в станкостроение, преобразует свою экономику в экономику высоких технологий. Так что со всех точек зрения совершенно очевидна необходимость приоритетного внимания к развитию отечественного станкостроения.
Вот только отрасль ныне пребывает в весьма плачевном состоянии. Входя в тройку лидеров среди мировых держав в конце прошлого века, сейчас мы уступаем не в разы, а в… десятилетия. В Россию завозится в три раза больше оборудования, чем производится внутри. Большая часть станкопарка составляет импорт. По утверждению эксперта, коэффициент обновления технологического оборудования в нашей стране составляет не более одного процента в год.
— Даже если считать, что парк станков в России составляет около 900 тысяч единиц, а более 70 процентов отечественных станков эксплуатируется свыше 15–-20 лет, при норме в два раза меньшей, и находится на грани полного физического износа, то при таких темпах на их обновление потребуется не одно десятилетие, — резюмировал Гутенев.
Был бы заказ
…Уже выходя из цеха, мы остановились у синей конструкции, напоминающей вагон метрополитена. Токарно-карусельный станок французского производства кабинетного типа с магазином инструментов прославился тем, что на нем изготавливали детали для адронного коллайдера. Станок был задействован и в военной промышленности — резал корпуса ракет. Но «француз», выпущенный в 1992 году, нагрузки не выдержал — отказала электронная часть. На предприятии специалистов не оказалось, и станок на много лет стал «недвижимостью».
— Мы его выкупили, — улыбается Александр Яшкин. — Это уникальный аппарат, который мы готовы реанимировать. Но чтобы восстанавливать станок, нам нужен заказчик с перечнем конкретных требований.
Возможности высокоточного универсального станка таковы, что достаточно установить заготовку, задать программу и получить готовое изделие. А вот что это будет, коллайдер или ракета, все зависит от заказчика.
Олег Гошев, фоторепортаж Вячеслава Шишкоедова
За помощь в организации фотосъемки благодарим ООО «Первая станкостроительная компания».
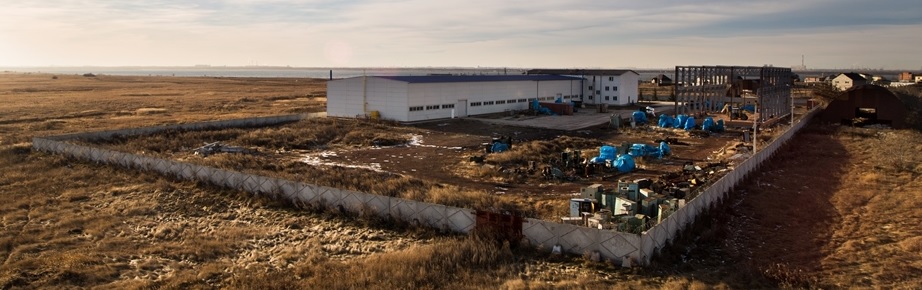